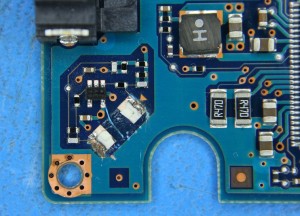
Our process works, and here's why
One of the many things we do when we receive a case for data recovery here at EADR is to send an email to the client acknowledging receipt of their device, and informing them of their unique case reference number. This is part of our ISO 9001:15 process. We also ask the client to provide us with some history on the hard drive and let us know how the failure occurred to their device and (more importantly to us) what recovery attempts have already been made. This is the email we received back from this particular client:“The hard disk drive is not powering up. The only attempt for data recovery was to remove the fuses from the board but that has not helped”.
Not quite right, but a brave attempt at repairing a hard drive nontheless!
Now, the eagle-eyed and more experienced reader will immediately notice that the main fuse (and there is only one) is still in place, so what exactly did the client remove? Well, if you look to the bottom left and the top right of the PCB (and the 2nd magnified image), located in those now vacant positions should be the ‘shock sensors’. These are the sometimes ‘pre-emptive’ sensors that detect if the drive is being dropped or in free-fall, and will automatically ‘park’ the heads (hopefully) prior to the impact on the drive, thus if not saving the actual heads, saving the precious data on the platters that should be undamaged in such a situation.
Needless to say, with this information the case was soon solved, and with some minor firmware works, the case was 100% recovered.
Just another day in the office at EADR... :)